Under a Microscope
The Examination of the Siege Scene Plate
Blythe McCarthy and Renata Holod
The Persian work known as the Siege Scene Plate (fig. 1), now in the collection of the Freer Gallery of Art, was found shattered in pieces. Dating to the first decades of the thirteenth century, it is an example of mina’i ware, a glazed stonepaste1 ceramic painted with many colors using at least two decorating and firing steps. Studies have revealed that the plate was reconstituted, likely during the 1920s and ‘30s, the heyday of the market for medieval Persian ceramics.2 In its restored state, the plate depicts the successful siege of a castle on its front and hunting feats on the back.
Because mina’i vessels have often been restored and repainted in this manner, a verification of their body and decoration must precede any full discussion of decoration.3 For this reason, examination of the plate was carried out in support of a research project by Renata Holod on the context and meaning of the siege scene and the circumstances of production of the plate.4 Close examination and cleaning of the surfaces have now permitted us to ascertain the plate’s original shape and the extent of its original decorative and pictorial program. Scientific analyses of the colorants and glazes have provided information about the methods and materials used to produce the plate.
The plate’s original body is made of artificial faience or stonepaste. Apart from the ring foot of the base, from which most of the glaze was removed prior to firing, it is completely covered with a white tin oxide opacified glaze, a perfect surface for painted decoration. The glaze has slightly pooled at its lower edge, on the exterior wall above the foot, indicating that it was fired upright. The usual cobalt blue, turquoise, red, and black, common on most mina’i/haft rang vessels is further augmented by magenta, a lighter cobalt blue, brown, and a flesh-colored, pinkish tone.5
Under the microscope, small fragments of gilding are visible on the wings of the central bird and on the shirt of the kneeling archer. They are too small to determine if they are gold leaf or gold paint. One could assume, however, that other, thematically more important areas in the plate’s imagery, such as depictions of victorious personages, would have been gilded also. Notably, all gilding observed in previous research on unrestored sherds in the Freer Study Collection was in the form of small squares of gold leaf.
The plate retains its original dimensions (diameter: 47.8 cm; height: 11.1 cm). Its size and shape are extraordinary among mina’i vessels, most of which tend to be smaller plates and bowls. Yet, it is not unique among other stonepaste wares. A series of at least eight plates (table 1) has the same range of dimensions and profile.
Table 1
Accession number |
Location |
Diameter (cm) |
Dated or dateable |
Reference (SPA = Survey of Persian Art) |
NEP19 |
University of Pennsylvania Museum of Archaeology and Anthropology, Philadelphia |
49.0 |
inscription dated 608 H/1211 CE at Kashan |
SPA , vol. 5, pl. 710 |
50/1966 |
David Collection, Copenhagen |
47.5 |
late 6th–early 7th H/end of 12th–early 13th century CE |
Arts of Islam , no. 34 |
32.52.2 |
Metropolitan Museum of Art, New York |
49.5 |
mid-7th H/mid-13th century CE |
SPA vol. 5, pl. 711 |
09.103 |
Museum of Fine Arts, Boston |
49.6 |
7th H/13th century CE |
SPA , vol. 5, pl. 711 |
1948.113 |
Cincinnati Museum of Art, former Kelekian Collection |
43.8 |
mid-7th H/mid-13th century CE |
SPA, vol. 5, pl. 712 |
British Museum, G.246, former Godman Collection, London |
49.0 |
7th H/13th century CE |
SPA , vol. 5, 640 |
|
1956-183 |
Ashmolean Museum, former Barlow Collection, Oxford |
47.3 |
7th H/13th century CE |
SPA , vol. 5, 641; Fehervari, no. 95 |
F1909.111 |
Freer Gallery of Art, Washington, DC |
47.5 |
late 7th–early 8th H/late 13th–early 14th century CE |
Atil 1973#, 69 |
All the plates on this list are decorated with luster painting, and only one, now in the Museum of Archaeology and Anthropology, University of Pennsylvania, has an inscribed date and provenance: 608 H/1211 CE at Kashan. (fig. 2a–c) The remaining plates are generally attributed to that famous Iranian center of ceramic production based on the style of their decoration6 and have been given approximate dates as listed above.7 In the latest of the series (fig. 3a–c), the rim is 2.5–3 cm in width, but the rim decoration extends onto the wall to a total width of 4.5–5 cm—similar to the width of the rim of the Siege Scene Plate. Profiles comparing the Siege Scene Plate with the earliest and latest plates listed in table 1 are shown in figure 4.
Considering how difficult it is to throw the friable stonepaste ware, the production of plates of this size and profile likely indicates another special skill of the Kashan workshop(s).8 These wares were prepared in pottery workshops and then decorated using a number of techniques, of which luster and mina’i were technically the most complex and artistically specialized. Caiger-Smith makes a useful distinction between the potters and the master painter-decorators, a distinction which is important to keep in mind when dealing with the Kashani tradition of decorating and image-making.9 In addition, Watson has proposed the supremacy (if not the monopoly) of the Kashan center in the production of luster on the Iranian plateau.10
Mason found a single petrofabric (the amount and size of mineral grains that collectively compose the ceramic, as seen in a thin section), which he assigns to Kashan, for all of the Iranian lusterware and mina’i pieces he studied. He associates the petrofabric with Kashan as the place of production through external evidence (i.e., signatures, dates, and place name of artist-decorators) from his studies of lusterware.11
The bulk composition of the base glaze for the Siege Scene Plate was analyzed on a microscale by laser ablation ICP-MS12 on a sample removed from one of the sherds with the foot. It was found to contain significant alkalies (sodium and potassium) as well as lead and tin (table 2).
Table 2. Composition of base glaze of Siege Scene Plate
SiO2 |
Na2O |
MgO |
Al2O3 |
P2O3 |
K2O |
CaO |
MnO |
Fe2O3 |
CuO |
SnO2 |
PbO2 |
57.43% |
6.36% |
1.74% |
1.32% |
0.09% |
3.19% |
2.87% |
0.03% |
0.42% |
0.11% |
7.60% |
17.84% |
Previous analyses of the white base glaze published by Mason et al.13 and Koss et al.14 indicate that the base glazes among mina’i wares were compositionally very similar. Their values are similar to those found for the Siege Scene Plate.
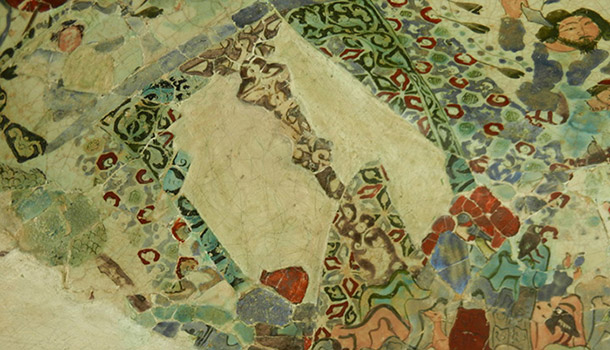
Figure 8a. View larger | View in new window
Surface Examination
X-rays and ultraviolet photographs show that the lower and upper left quadrants are the most fragmented, and consequently the most restored, parts of the plate. (figs. 5, 6, 7) Cleaning the surface during the conservation treatment removed all overpaint that covered original elements. During this process, Lynda Zycherman noted that there were possibly three levels of repair with materials including hide glue, PVA, and both white and pink plasters. She observed that one area of pink plaster had been broken and repaired prior to the plate’s arrival at the Freer.15 After the initial examination, fills were painted to match the base color of the glaze. Only minimal inpainting was carried out; areas with inscriptions or figures were not inpainted.
The examination has established that, in addition to the plaster fill material applied as part of the repairs, the individual sherds used to reconstitute the plate came from several different sources. Many are from the original plate, to be sure, but others were chosen to match adjacent ornaments as closely as possible, at times completing or enhancing a design. Nonetheless, their curvature is slightly different, which is perceptible to the naked eye and by touch. This is seen on the obverse of the plate in both the central panel of the fortress revetment and the landscape below, and on the reverse of the plate in the floriated Kufic inscriptions and the feline, to name just a few examples. (figs. 8, 9, 10) Also, in some places restorers inlaid a half-thickness sherd with an approximately matching motif. This is seen in the tree branches (fig. 11a–b) on both sides of the plate. In the x-rays, inlaid sherds can be identified when their shape or curvature does not carry through to the opposite side of the ceramic.
To facilitate a detailed description of the plate in its current, post-conservation state, we have used the convention of reading the plate from center to rim, beginning with the bird in the center and proceeding down and clockwise around the walls and rim. Continuing outward, we marked every sherd that had a clean join. In marking the sherds, the following conventions were used: (fig. 12a–b)
Red: Correct and original to this plate (fig. 13a–b)
Pink: Most likely original to this plate but not necessarily in the correct location (fig. 14a–b)
Green: Inset sherds visible from both or only one side, possibly from this plate (fig. 15a–b)
Purple: Inset sherds definitely not from this plate (fig. 16a–b)
Blue: Painted fill material
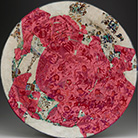
Figure 13.
Enlarge | New window
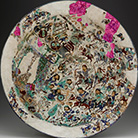
Figure 14.
Enlarge | New window

Figure 15.
Enlarge | New window
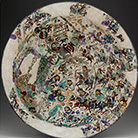
Figure 16.
Enlarge | New window
Obverse
Three large sherds comprise the base of the plate. The central scene on the base is correct and original with the exception of an inset sherd that replaces the proper right cheek of the archer of the first row of the sortie group. This area includes all the victorious horsemen (fig. 17) as well as the walls of the fortress with an archer in a gallery, and armor arranged on the parapet of the fortress. Continuing down and to the right, the plate decoration is correct and original to the rim with only one inset triangular sherd that replaces the proper left arm of a foot soldier behind the named horseman Amīr Sābiq al-Dīn. This area of correct and original sherds includes all the named horsemen and the battle on the rim.
Proceeding clockwise, there is a large area of restoration that extends to the rim. At the shoulder of the rim the landscape begins, which is made up of many sherds. The right portion of the tree with a bird is correct and original, including the bird and the upper portion of the trunk. The left side, bottom of the trunk, and upper tip of the tree are formed from inset sherds. Inset sherds continue the landscape, forming a second tree to the left, and create legs for the kneeling lowermost swordsman of the sortie group in the central scene.
Unconnected to the correct and original sherds carrying the inscription on the rim is a single inset sherd with the head of a horse, inserted at the next section of the rim after the large fill. The remainder of this rim section, including all with the inscription, can be directly linked together to the mountainous landscape and to one sherd of the second tree’s trunk. In turn, it can be tied to the base of the plate through the design of the fortress. All this is correct and original. The footing of the right edge of the wall is composed of several small inset sherds and does not extend to the landscape.
The wall decoration in the center rises from the footing but does not continue into the center from the lower part of the column. Significantly, the rest of the column is formed of inset sherds. There are large fills to either side of this composed column. The left wall of the castle is also composed of multiple small sherds; however, enough of the original remains to place the end of the building and the gallery with the lower body of the rear archer. The head is inset. The top and bottom of the tree greenery are correct and original, while the center and lower trunk are composed of inset sherds. Two small rim sherds are not original but are connected with a small horseman, who is most likely correct and original.
After a small area of fill, the rim continues with two full and two partial horsemen that are correct and original. The adjacent area with the siege machine/catapult is correct and original, as are the feet and hindquarter of the elephant visible above the crenellations of the fortress. The remainder of the elephant’s body is made up of multiple inset sherds. The head of the elephant is attached to a group of rim sherds with soldiers, which fit the rim profile and are likely correct. Continuing around the rim is an area with horsemen, which cannot be directly connected to the central scene but follows in terms of design and rim profile and is likely correct and original. This area is also connected to the drummer boy and partial horseman on the wall of the plate. To its left is a single triangular rim sherd with the partial head of a man that is not correct.
To the right and surrounded by an area of fill is a single large sherd of a horseman that is not correct. Below and to the left are several isolated sherds of flowering branches, a bird flying parallel to the rim, and the head of the horseman below; all are not correct. Underneath the sherd with the drummer is an unconnected sherd with a second bird. The next area of rim is correct and original and can be directly associated through the horsemen to the base. It is followed by two small rim sherds that have partial faces of men and are not correct. With the exception of the floating flowers and birds, the replacement sherds complete design elements for which there is evidence from other mina’i wares, but in themselves are not correct and original.16
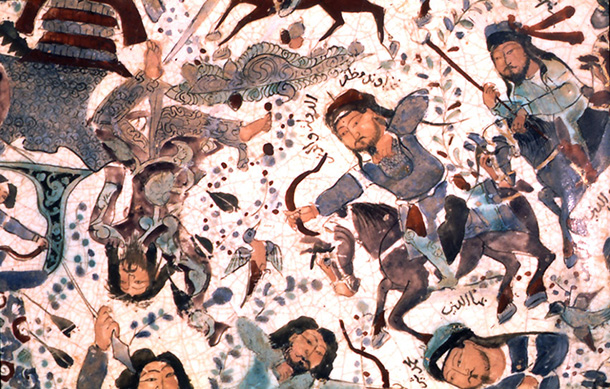
Figure 17. View larger | View in new window
Reverse
The footring is complete and original, as is the foot with the exception of a small triangular fill at the center. The complete and original rim segments are decorated with an inscription in floriated Kufic. Great effort has been made to match this motif by assembling similarly decorated sherds from other mina’i vessels.
The red feline in the lower left quadrant has its correct and original head, back, and rear legs, while the forepaw and underbelly are composed of several cut-to-shape red fragments. Proceeding clockwise, the lower half of the flowering tree to the left of the feline is on the same sherd as the feline’s head and back; the upper half of the tree is continuous. The rim in this area is a restoration. The original and correct rim begins again above the head of the hero with a mace. The bottom of the beard is missing, as is a triangular area of his chest. There is also a small loss to the foot, but the remainder of the figure is complete. Above the proper left shoulder of the figure is a small inset sherd of foliage. The bird is missing its head but the body is correct and original.
The rim continues until just beyond the archer’s head. The vessel wall in this area is complete and original. A rectangular piece of floriated Kufic is inset from another piece; the script is of a smaller scale than that of this plate. The next small sherd at the edge of the rim is not connected to any other sherd and may not be correct. The bird above the archer’s bow is correct, as are the tree branches that are on that same sherd. Behind the archer is a figure standing under a tree. The head of the figure is an inset, but the remainder is correct and original. The lower portion of the tree trunk is correct, but the middle and upper portion, as well as the foliage directly above, are composed of multiple pieces that cannot be directly tied to the vessel foot.
Above the tree, the rim is correct and original. Next to this area are two small sherds that do not match the script. The bottom of the dragon’s tail, a hand, and the hilt of a sword are correct and original. The only other portion of this hero, which is still correct and original, are his red boots; the rest is probably original, but not in the right location. A sherd extends down from the rim with the dragon’s snout. While it cannot be linked to the foot, it shares both the decoration and profile of this plate and is probably original.
The landscape elements behind the figures are correct and original. Within a flowering tree are four birds. The bird toward the rim at left is an insert; the other three birds are correct and original. The cypress tree to the right has a bird at its center; there is a loss to the upper portion of the bird that extends slightly beyond the tree to the right. Above the trees, the rim is composed of several fragments, either possibly or certainly from other vessels. The rim can again be linked to the foot past the bovine-headed mace held by the hero. This area, encompassing the quadruped and the hero with a mace and ending with a small flowering branch and the proper right turquoise-patterned sleeve and hand of the next figure, is correct and original. The bird between the two figures and the calligraphic rim section above is correct and original to the plate.
From the turquoise sleeve through the rim, the design is connected to the hat and hair of the second figure as well as to the proper left sleeve and hand and adjacent foliage. These elements are surrounded by areas of fill. The face and central portion of the figure are missing, although two feet are visible at the edge of one of the large sherds composing the vessel base. Further along the edge of the base sherd are landscape elements, an animal leg, and a human foot. The remainder of the design cannot be conclusively associated with this object as it does not attach to other pieces; however, there is one large area inclusive of rim with a bowman as well as two trees, three birds, and the neck of a griffin. This section appears to have the same design and profile for the rim. Foliage of a different type follows which, along with the two small sherds above it at the center of the rim, are either placed incorrectly or come from another object.
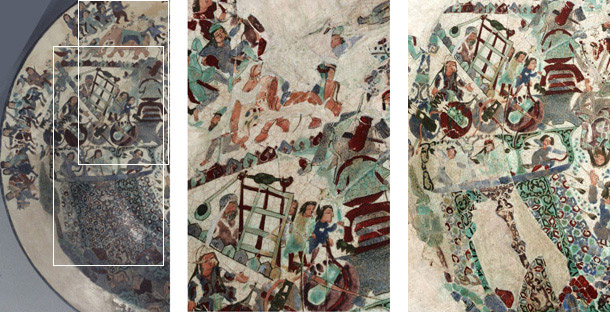
Figure 18. View larger | View in new window
Summary of the Surface Examination
The main elements of the siege scene are original. The details of auxiliary areas such as those on the lower and upper left quadrants had been repainted and therefore were removed during conservation treatment. (fig. 18) Removed areas are not included in the above description.
Every letter of the inscriptions has been verified. Accordingly, the reading of the names and the inscription on the rim has been enhanced, as discussed by Holod.17 This examination highlights the outstanding craftsmanship of pottery production and highly skilled drawing involved in the making of the plate.
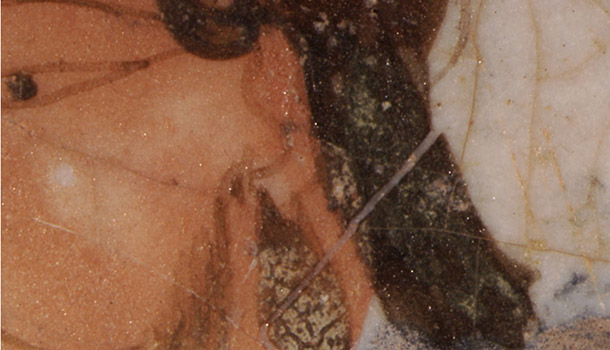
Figure 19a. View larger | View in new window
Painting Technique
The complex pictorial program of the plate’s obverse, while assembled out of elements already utilized in the local decorating traditions, was carefully composed through underdrawing. Traces of such a technique are clearest on the figures’ faces, but also seen on clothing and in the animals, landscape elements, and other features. (fig. 19a–b) They indicate that a preparatory sketch (or sketches) was applied on the once-fired white glazed surface prior to the application of the magenta, red, and flesh- colored glazes. In one area, the foot of a soldier has been reworked in the final drawing. (fig. 20)
Preparatory drawing is known from later Persian painting practice. It is visible in particular on incomplete paintings on paper. For example, see the upper-right corner of An Assault of a Castle, attributed to Bihzad (fig. 21) (Harvard University Museums, 1960.199);Solomon and his Court, a folio from a manuscript painted in the circle of Mirza ‘Ali ca. 1560 (Harvard University Museums, 2011.540); and the unfinished Garden Scene (Cleveland Museum of Art, 1944.490.a). Further, preparatory drawings from Timurid and early Safavid workshops are now located in albums such as the Bahram Mirza Album (Topkapı Palace Museum, H. 2154).18 Current study of the workshops that produced the paintings and sketches has indicated that the practice of assembling scenes out of existing corpora of types and vignettes was standard workshop practice.
The existence of underdrawing on the plate itself, then, would point to the longstanding nature of this practice. Preparatory materials, whether sketches or even pounces,19 would have been utilized to compose the main image on the obverse and even the more stock images of the heroes on the reverse. Even if no underdrawing is visible today in areas with colors fired in the first firing cycle (turquoise, dark blue, light blue), an initial preparatory drawing could still have been a possible practice as carbon black would not have discolored the glaze and would have been lost during firing.
Underdrawing for vessels with complex decoration appears to have been common, although often visible only under close examination. Both black (composed of an iron-chromium oxide, as in the Siege Scene Plate) and red (composed of iron silicates) underdrawings have been observed on other mina’i examples.20 In line with the practice of later Persian painting ateliers, a final overdrawing reinforces the key features of the initial design and mostly follows the underdrawing. On the Siege Scene Plate, this last step was not quite completed, as some members of the victorious army are lacking lances and bowstrings.21
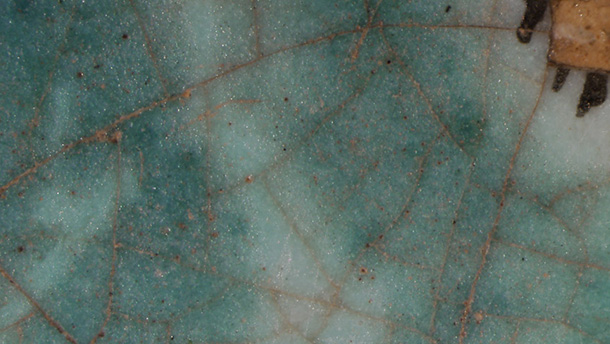
Figure 24. View larger | View in new window
Colors
The degree of polychromy and the control over the colors on the surface of the Siege Scene Plate is unusual among mina’i vessels.22 On the obverse, the plate has dark and light cobalt blues, turquoise, black, red, magenta, brown, flesh color, and one instance of a light flesh color (fig. 22), while the reverse has dark and light cobalt blues, turquoise, flesh, black, red, magenta, brown, and an olive green. More typically, examples from this group or production type are limited to two colors (cobalt blue, turquoise) applied over the raw base glaze prior to firing.23 All other colors were applied after an initial firing step, as part of a subsequent decorating and firing cycle or cycles.
On most examples, the demarcations between color zones for the cobalt blue and turquoise are not well maintained, and the final black outline drawing is often carelessly applied. The colors fired with the base glaze typically penetrate into the white surface, and those fired in the second firing sit on the surface of the white glaze. In the Siege Scene Plate, the turquoise and dark blue were applied with the first firing. The magenta, flesh color, red, black, and brown appear to have been fired in the second firing. It is likely, however, that this was not a rigid process, and variations in the layering of the colors even within a single object suggest that the artist may have at times applied colors with multiple firing steps. For example, the light blue appears to have been painted in areas under the dark blue, indicating firing in the initial step, but in other areas it is over the red, suggesting a later firing.
The two-step firing process of the Siege Scene Plate is similar to that seen in previous studies on other mina’i ceramics. For example, Mason et al. demonstrate that certain colors may be fired with the base glaze (blue, black, and brown) while other colors, including cobalt blue, tin oxide white, red, and black, are applied after the initial firing.24 Koss et al. expanded on that study to determine that cobalt blue and flesh color may be either fired with the base glaze or in a later firing, while the turquoise is only found fired with the base glaze.25 Colors fired with the base glaze diffuse into it, coloring the white glaze. This is particularly noticeable for the turquoise in this plate, whereas the colors fired later have a sharp interface with the underlying glaze (fig. 23) that can be seen in cross-section under the microscope and are often raised above the surface.
At break edges of the Siege Scene Plate and in cross-section, both the turquoise and dark blue can be seen penetrating the glaze. For these two colors, the artist maintained a clear separation between areas of application to ensure that they would not mix, a real possibility given their movement. By looking closely at the surface, it is readily apparent that the turquoise colorant, copper, has diffused into the opaque white glaze. The turquoise is surrounded by a green haze that has extended beyond the edge of the initial application area. (fig. 24) For the dark and light blues, no defined interface with the white glaze is visible on break edges or in cross-section (fig. 25); however, the color does not appear to penetrate as far into the white glaze as the turquoise.
The olive green on the reverse is formed by a thin layer with high chromium, potassium, iron, and lead above the turquoise. (fig. 26a–b) This color is not found on the obverse of the plate. Chromium, lead, iron, and potassium are increased at the top edge of the layer. It is not clear whether an iron chromate wash was applied to these turquoise areas, or whether separation of the components occurred during application and firing. The green tint resulting from the chromium is original to the process of decoration, however, and is not a product of degradation processes.
Colorants were determined by XRF for all the colors are listed in table 3. Lead and tin were seen in every spectrum, but are not included in the table as it is unclear if they are present in the color or in the underlying base glaze. Small peaks are indicated in parentheses.
Table 3. XRF Analysis of Colorants
Color |
Elements determined by XRF |
turquoise |
copper, iron, (chromium) |
dark blue |
cobalt, iron, copper, chromium, (arsenic) |
light blue |
iron, cobalt, copper, (arsenic, chromium, manganese) |
magenta |
manganese, iron, copper, (zinc) |
red, exterior |
iron, (copper, chromium) |
black |
iron, manganese, chromium, copper |
brown |
iron, chromium, copper, (zinc, manganese) |
flesh color |
iron, copper, increased tin |
olive (exterior) |
iron, chromium, (copper, zinc) |
white glaze |
lead, tin, copper, iron |
The use of two shades of cobalt blue as seen on this plate is unusual. Study of other mina’i undertaken by the Freer|Sackler Department of Conservation and Scientific Research (DCSR) has shown that, although the shade of a specific color may vary from ceramic to ceramic, on a single vessel the number of glaze colors is limited and variations in shades generally are not visible. This is an indication that the control of the production process was not at the level that could produce a nuanced image for the majority of the mina’i production. Other examples of multiple colors of cobalt blue occur on the well-known tile at the Museum of Fine Arts, Boston (31.495), titled Iranians leaving the fortress of Farud,26 and on a tile showing Rustam and the dragon in the Freer (F1911.319).27 (fig. 27)
The dark blue contains the same elements (cobalt, iron, copper, chromium, arsenic) as the light blue, just in different proportions. (fig. 28) In the XRF analysis the peak heights were ratioed to the lead peak height: Cobalt and chromium both increased for the dark blue (chromium by a factor of ten) while the copper and arsenic stayed about the same and the iron decreased. This finding suggests that either a different grade of cobalt was used for the dark blue than the light blue, one containing more chromium, or that the cobalt contained or was mixed with a chromium mineral. In addition to the higher cobalt concentration, the black chromium mineral acts to darken the blue color. The dark blue areas have scattered dark particles (fig. 29a) and many large bubbles (fig. 29b), indicating that the components include cobalt mineral, here only partially dissolved, as well as salts, which would have decomposed during firing to form bubbles and interacted with glass-forming minerals to produce the glass matrix of the color.
On this plate, magenta is very thinly applied and has diffused slightly into the base glaze. Yet, it lacks a surrounding haze, has a defined interface with the white base glaze (fig. 30a–b), and exhibits shrinkage “T” cracks (fig. 31) typical of drying on an inflexible surface, i.e., a fired glaze. From close examination, it is clear that here it was applied in the second firing and, at least in some areas, later than the red.28 (fig. 32) The pinkish flesh color is composed of a mixture of tin oxide with iron oxide and a glass phase composed of either a glass frit or glass-forming minerals and salts.29 There is more tin oxide than in the base glaze (see fig. 23), indicating that tin oxide was added separately and is not present simply due to admixture with the base glaze powder.
The red is composed of iron silicates with a glass phase and the black of iron chromates. Both have a sharp interface with the base glaze visible at the break edges and have not extended beyond their boundaries on the surface. (fig. 33) The brown, used sparingly on the hats of the victors on the obverse and of the hero on the reverse, was fired in second firing. It is thinly applied and has sharply defined edges. (fig. 34) Some gradation in the colors can be caused by both the atmosphere in the kiln during firing and later degradation processes. The amount of oxygen in the atmosphere of the kiln can affect the oxidation state of the transition metal colorants. For example, variations in the manganese oxidation state can result in a range of shades from magenta to a violet-brown.30 Similarly, differences in the iron oxidation state, as well as the presence of additional elements, can result in red shades ranging from bright red to a reddish brown. These differences generally do not result in variations in color on a single mina’i ware; however, they may account for color variations between wares. Firing variations are visible in the Siege Scene Plate in the blacks that at times can have a greenish-gray hue. (fig. 35)
Both chemical and mechanical degradation of the glaze can also affect the colors. Small cracks that form at the surface and the loss of glaze fragments on a microscale can increase surface roughness. This results in loss of gloss, lightening of the colors, and an increase in opacity. Such an effect is visible on the dark blues of the Siege Scene Plate, where the high number of broken bubbles in the glaze has increased the propensity for discoloration and material loss. (see fig. 29)
Black Accents and Finishing Touches
Accents mark both sides of the Siege Scene Plate, in a black that appears gray-green or both black and gray-green. (figs. 36 and 37) Cobalt has been found with chromium in black areas on the plate. With small amounts of cobalt, an iron-chromate glaze can appear bright black; without cobalt, gray-green. Copper, in the turquoise areas, also affects the color. Under magnification, the black accents are clearly above the other colors, indicating that they were applied as one of the last steps, if not the last step, in the decorating process, used to outline figures and put in facial features and other details. As noted earlier, this process was not completed on all areas of the obverse.
Types of Mina’i
The cited studies and an examination of large numbers of mina’i vessels and sherds provide information on at least two techniques for applying decoration. First, in the wares with many colors, like this plate, one finds turquoise, light blue, and dark blue fired with the base glaze and the remainder of the colors fired in second firing(s). A second type of mina’i ware has a more limited color palette, with all colors fired after the initial firing of the base glaze. This latter type could be identified with Abu Zayd and his group active from the 1180s onward.31 In a subset of wares of this type with similar geometric designs analyzed by Koss et al., the cobalt blues were found to contain higher levels of arsenic, at 3–5 percent, than seen in any of the other cobalt blues, suggesting these were made in a different workshop, or at another time.32
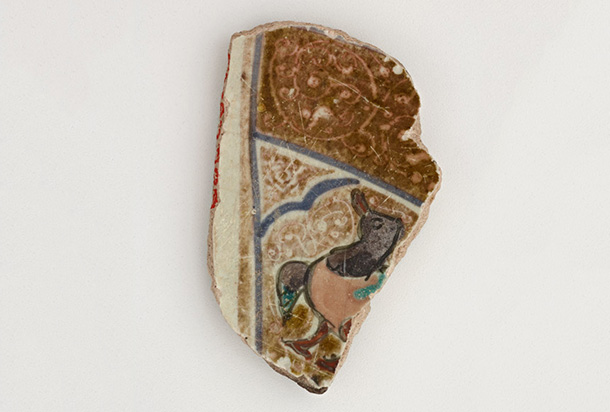
Figure 38. View larger | View in new window
Relation to Other Ceramics
Many examples of lusterwares are seen with turquoise and cobalt blue accents. These share the characteristics of the same colors used in mina’i: diffuse edges, particularly in the turquoise, and a flat profile. One example of this luster technique is a tile, with the addition of turquoise and cobalt on areas of relief, from a mihrab, now in the Freer Gallery collection (F1909.319).33 A luster and mina’i sherd (FSC-P-4804) analyzed by the DCSR had a cobalt blue fired in the second firing step, however. (fig. 38) Analysis of a wider range of materials is necessary to understand more fully the variability in this technology. Examination to date has shown that subject and technique have no direct correlation.
Further, Koss et al. examined multicolor mina’i sherds and tiles, including “lajvardina” examples similar to those from Takht-i Sulaiman, as well as some later so-called “enameled” wares.34 The study showed that there are only slight differences in the techniques used to decorate these ware types, suggesting a relationship and continuity of workshop practices between them. Considering lajvardina as a ware type separate from mina’i in particular seems to be an artificial division, based more on appellations used by the antiquities market than on terms contemporary with their manufacture. While the lajvardina type produced into the fourteenth century has a blue base glaze, it also has a two-step firing process to complete its decorative program. It should perhaps be seen as a continuing variant type of mina’i ware. Mina’i and lajvardina appear to share related production practices and a technological process that maintains room for creativity, variability, and developments to meet changes in taste or market demand.
Conclusions
This examination has resulted in a better understanding of Freer’s Siege Scene Plate in terms of its materials and original production. Documenting the original surface from the more than three hundred sherds that now compose the restored plate has allowed the surface and decoration of the plate to be examined and interpreted.
The main iconographic elements of the Siege Scene Plate are original. Every letter of the inscriptions now has been verified, supporting a more complete reading. Further, this examination highlighted artisans’ outstanding control over the mina’i enameling procedure, as well as the artistic process involved in the decoration of the plate.
The complex imagery of the obverse, while assembled of elements that were part of the local visual culture and decorating traditions, was carefully composed through the use of underdrawing. The degree of polychromy and the control over the colors on the surface is unusual among mina’i vessels. Close examination has revealed the sequence of colors applied either on the raw glaze prior to the first firing or as part of the subsequent phase (or phases). The final black outline drawing, although incomplete in small areas of the obverse scene, is executed with skill and care.
Figures
Figure 1. Siege Scene Plate showing multiple post-cleaning views; Iran, Saljuq period; ceramic, D: 47.8, H: 11.1 cm; Freer Gallery of Art, F1943.3.
Figure 2a–c. Three views of luster plate; Iran, 608 H/1211 CE; ceramic, D: 49, H: 11 cm; Museum of Archaeology and Anthropology, University of Pennsylvania, NEP 19.
Figure 3a–c. Three views of luster plate; Iran, Saljuq period; ceramic, D: 47.5, H: 11.6 cm; Freer Gallery of Art, F1909.111.
Figure 4a–c. Composite drawing of plate profiles including Museum of Archaeology and Anthropology, University of Pennsylvania, NEP 19; Freer Gallery of Art, F1943.3; and Freer Gallery of Art, F1909.111. Drawing by Kimberly Leaman.
Figure 5. Siege Scene Plate showing pre-cleaning views of obverse and reverse.
Figure 6. X-ray radiograph of Siege Scene Plate showing the more than 300 pieces composing the plate as well as superimposed sherds (which indicate that they were inlaid).
Figure 7. Siege Scene Plate showing pre-cleaning views of obverse and reverse under ultraviolet illumination.
Figure 8a–b. Detail of fortress and landscape beneath the fortress on the obverse of the Siege Scene Plate.
Figure 9. Detail of floriated Kufic on the reverse of the Siege Scene Plate.
Figure 10. Detail of lion on the reverse of the Siege Scene Plate.
Figure 11a–b. Detail of inset flowers and tree branches on both sides of the Siege Scene Plate.
Figure 12a–b. Overlay indicating authenticity of sherds on both sides of the Siege Scene Plate. Red is original, pink may be original, green is misplaced, purple is from another vessel, and blue is fill.
Figure 13. Overlay of correct and original sherds in red on both sides of the Siege Scene Plate.
Figure 14a–b. Overlay of possibly original sherds in pink on both sides of the Siege Scene Plate.
Figure 15a–b. Overlay of sherds that are misplaced or possibly from another vessel in green on both sides of the Siege Scene Plate.
Figure 16a–b. Overlay of sherds from another vessel in purple on both sides of the Siege Scene Plate.
Figure 17. Detail of central scene on the obverse of the Siege Scene Plate.
Figure 18a–b. Pre- and post-cleaning details from proper right side of the Siege Scene Plate.
Figure 19a. Detail of the face of the victor, Lord (khudāvand) Muzaffar al-Dawla wa’l-Dīn, on the obverse, showing underdrawing and final drawing. b. Detail of a canine showing underdrawing on the reverse of the Siege Scene Plate.
Figure 20. Detail on the rim with underdrawing and final drawing.
Figure 21. Example of an unfinished painting: Attributed to Bihzad, Assault on a Castle, ca. 1475–1500. Opaque watercolor and gold on paper; image with border: 33.5 x 22.5 cm (13 3/16 x 8 7/8 in.), Harvard Art Museums/Arthur M. Sackler Museum, Bequest of Abby Aldrich Rockefeller, 1960.199. Photo: Imaging Department, copyright: President and Fellows of Harvard College.
Figure 22. Detail of figure showing two shades of flesh color on the obverse of the Siege Scene Plate.
Figure 23a–b. Left to right: An optical microscope image and backscattered electron image show the well-defined interface between the flesh color and white in the cross-section of flesh-colored glaze from the dragon on the reverse. This is characteristic of layers applied after an initial firing.
Figure 24. Detail showing turquoise haze on the obverse of the Siege Scene Plate.
Figure 25a–b. Cross-section of light blue glaze on the plate. Blue is at the top edge of the sample in the optical microscope image (left). The extent of its penetration into the white glaze can be tracked through precipitates that appear dark in the backscattered electron image (right).
Figure 26a–b. Left to right: An optical microscope image and backscattered electron image show a cross-section of turquoise glaze from the mountain on the reverse of the plate with black on top. Discoloration of the turquoise is due to iron chromate particles in the black.
Figure 27. Tile showing Rustam and the dragon; Iran, Saljuq period; ceramic, 18.3 x 1.7 cm; Freer Gallery of Art, F1911.319.
Figure 28. XRF spectra of light and dark blue on the Siege Scene Plate, taken at 45 KV, .50 mA, for 100 live seconds in air.
Figure 29a–b. Detail of dark blue areas with scattered dark particles that are the undissolved portion of the cobalt mineral colorant (left), and bubbles formed during firing from reaction of the colorant mixture (right).
Figure 30. Left to right: An optical microscope image and backscattered electron image show a cross-section of the magenta colored area.
Figure 31. Detail of magenta colored area showing shrinkage cracks.
Figure 32. Detail of magenta glaze applied over flesh color and red.
Figure 33. Detail of red showing pooling at edge of drop that indicates application on a non-porous surface.
Figure 34. Detail of victor on the obverse of the Siege Scene Plate.
Figure 35. Detail showing black with green-gray hue on the reverse.
Figure 36. Detail of hat on the reverse of the Siege Scene Plate.
Figure 37. Detail of a black line that changed color on turquoise glaze on the reverse of the Siege Scene Plate.
Figure 38. A sherd decorated with luster and mina’i. It contains a cobalt blue determined to be applied after the initial firing step. Iran, Saljuq period; ceramic, 4.7 x 3.8 x 0.6 cm; Freer Gallery of Art, FSC-P-4804.
Tables
Table 1. List of Large Plates (end of 12th–14th century)
Table 2. Composition of base glaze of Freer Siege Scene Plate
Table 3. X-ray Fluorescence Analysis of Colorants
About the Authors
Blythe McCarthy is Andrew W. Mellon Senior Scientist at the Freer Gallery of Art and Arthur M. Sackler Gallery, where she has been on staff since 1998. Prior to that she held fellowships at the Getty Conservation Institute and The Fraunhofer Institute for Silicate Science. Her research interests include the technical study of artists’ materials, and the development of nondestructive techniques for their analysis. She is a professional associate of the American Institute for Conservation and recently was awarded a FAIC/Samuel H. Kress Conservation Publication Fellowship to complete a book on Chinese pigments based on research records held at the Freer|Sackler. Email: mccarbl@si.edu
Renata Holod is College for Women Class of 1963 Professor in the Humanities in the History of Art Department and curator, Near East Section, the Museum of Archaeology and Anthropology, at the University of Pennsylvania. Her publications include The Mosque and the Modern World (1997) and An Island Through Time: Jerba Studies (2009 and forthcoming), and she co-edited The City in the Islamic World (2008). She has served as convenor of the Aga Khan Award for Architecture, and as Clark Professor at the Clark Art Institute and Williams College. Her current project is a collaborative investigation of the grave goods of a Qipchaq kurgan. Most recently, she investigated the historical and art-historical context and meaning of Freer’s Siege Scene Plate for Ars Orientalis. Email: rholod@sas.upenn.edu
Endnotes
[1] After the description by Hans E. Wulff in The Traditional Crafts of Persia: Their Development, Technology and Influence on Eastern and Western Civilizations (Cambridge: M.I.T. Press, 1966), 165, of the techniques of the “stonepaste potters,” the atīqeh-sāz or sangīneh-sāz of Isfahan, Natanz, Kashan, and Qom, the term “stonepaste” was generally adopted to describe a ceramic body formed of a mixture containing silica with minor amounts of silicate minerals, clay, alkalies, and/or glass. A typical recipe, as given by Wulff, is 70–80 percent quartz, 10–20 percent of very fine clay, and 10 percent of a frit (finely ground glass). The term “stonepaste” has been used extensively in the literature on ceramics from Iran, Syria, and Egypt. For example, see Robert B. Mason, Shine Like the Sun. Lustre -Painted and Associated Pottery from the Medieval Middle East (Costa Mesa, CA: Mazda Publishers, Inc. in association with Royal Ontario Museum, 2004), 73, 94, 123; and most recently, Stephen Mc Phillips, “Continuity and Innovation in Syrian Artisanal Traditions of the Ninth to Thirteenth Centuries: Ceramic Evidence from the Syrian-French Citadel of Damascus Excavations,” Bulletin d’ Etudes Orientales 61/2012, 447-474.
[2] Further examination of the first accession dates of mina’i ceramics in museum collections would likely show that most of the best-known pieces first came on the market from the 1910s through the 1930s. See, for example, the collection of the Museum of Fine Arts, Boston, where mina’i pieces have accession numbers dating from 1917 through 1938. On fashions in collecting ceramics, see Oliver Watson, Ceramics from Islamic Lands (London: Thames and Hudson, 2004) 14–19. The popularity of mina’i acquisitions also may have been connected with the commercial antiquarian firms with branches in Tehran and Paris, and with the promotional activities of Arthur Upham Pope; see collected essays in the study Arthur Upham Pope and a New Survey of Persian Art, ed. Yuka Kadoi (Leiden: Brill, forthcoming). We thank Judith Lerner for this reference.
[3] For a discussion of the authenticity of mina’i pieces and the frequent practice of assembling a vessel out of several fragmentary ones, see Ernst Grube, Islamic Pottery of the Eighth to the Fifteenth Century in the Keir Collection (London: Faber and Faber Limited, 1976), 195, note 1; and more recently, Kirsty Norman in Watson, Ceramics, 2004, 71–89. Dr. Lisa Golombek (now Curator Emerita) of the Royal Ontario Museum, Toronto, first alerted Holod to the inlaying practice of restorers and made available her examination records of mina’i pieces under her care. The original inspection of the Siege Scene Plate at the Freer Gallery was carried out with the participation of Dr. John Winter and Lynda Zycherman of the Freer Technical Laboratory, and Dr. Esin Atil, then curator of Islamic art.
[4] For the results of the study, see Renata Holod, “Event and Memory: The Freer Gallery’s Siege Scene Plate,” Ars Orientalis 42, 194–219.
[5] Holod has been able to study mina’i objects and sherds in detail in the collections of the Freer Gallery of Art, Washington, D.C.; the Walters Museum, Baltimore; the Metropolitan Museum of Art, New York; the Museum of Fine Arts, Boston; and the University of Pennsylvania Museum of Archaeology and Anthropology. Other collections of mina’i pieces that were inspected include those at the Victoria and Albert Museum, London; the Ashmolean Museum, Oxford; Muze Iran Bastan, Tehran; and the Khanenko Museum, Kyiv. McCarthy has been able to study mina’i objects and sherds at the Freer Gallery of Art; the Walters Art Museum; the Sèvres Museum, Paris; and the Metropolitan Museum of Art. We thank all the past and current curators of these institutions for allowing access to their mina’i collections, and Massumeh Farhad, chief curator of the Freer and Sackler Galleries, for supporting our efforts. Gail Yano and Sydney Williams are thanked for their help with determining sherd locations.
[6] Geza Fehervari, Islamic Pottery. A Comprehensive Study Based on the Barlow Collection (London: Faber and Faber Limited, 1973), no. 95, attributes the Ashmolean Museum plate [acc. no. 1956-183] to Rayy, a customary attribution, but with no actual proof. None of the plates on the list have been tested for petrographic composition. On the discussion of Kashan as a production center and Kashan petrofabric, see Mason, 2004, 140–42.
[7] The Freer Siege Scene Plate was TL dated by the Research Laboratory for Archaeology at Oxford University in 1973. The result was between 360 and 790 years ago.
[8] The dated piece from the Penn Museum (NEP19), as well as the Freer luster plate (F1909.111), for example, are quite deformed as is visible from the appended photographs. Mason, Shine, 2004, 150–53 gives a useful range of large plate profiles in his tables of Kashan luster groups 1 through 10, and on page 154 provides a typological and chronological layout. In particular, the profiles of the large plates (ASH 10) and (ASH 45) are close comparisons.
[9] A. Caiger-Smith, Lustre Pottery Technique, Tradition, and Innovation in Islam and the Western World (London and Boston: Faber and Faber, 1985), 139.
[10] Oliver Watson, “Documentary Mina’i and Abu Zaid’s Bowls,” in ed. R. Hillenbrand, Art of the Saljuqs in Iran and Anatolia (Costa Mesa, CA: Mazda, 1985), 170–80; and Watson, Ceramics, 2004, 347–63. See Mehdi Bahrami, Gurgan Faiences (Cairo: Le Scribe Egyptien, 1949) and Yusuf Kiani, The Islamic City of Gurgan (Berlin: D. Reimer, 1984) on the Gurgan (medieval Jurjan) workshop, although the prevalent shapes found there are small and do not achieve the kind of technical mastery in production nor sophistication in decoration seen in the Kashan production. Also, since the ceramic material was found stored in large jars, it has been argued that this was the stock of a merchant hidden from the Mongol onslaught rather than a workshop site; see Oya Pancaroğlu, Perpetual Glory (Chicago: Art Institute of Chicago, 2007), cat. #80,124.
[11] Mason, Shine, 2004, 179 and 206.
[12] The analysis was carried out at the LA-ICP-MS Laboratory, Department of Anthropology, Field Museum of Natural History, Chicago, with help from Laure Dussubieux under NSF grant #0818401. A sample removed from the exterior glaze on one of the large sherds that includes part of the foot was analyzed using laser ablation ICP-MS using a Varian ICP-MS coupled with a New Wave Research UP 213 laser system for direct introduction of solid samples. A pre-ablation pass line to clear out surface contamination was made at ca. 500 µm long and 100 µm wide, at 70 µm/s at a frequency of 20 Hz; and an actual ablation pass line that was 500 µm long and 65 µm wide, at 5 µm/s, and at a frequency of 15 Hz was made in the same location. The isotope Si29 was used for internal standardization and SRM 610, SRM 612 and Corning Glasses B and D were used for calibration.
[13] Mason, R. B., M. S. Tite, S. Paynter, and C. Salter, “Advances in Polychrome Ceramics in the Islamic World of the 12th century AD.” Archaeometry 43(2)/2001, 191–209.
[14] Koss, K., B. McCarthy, E.S. Chase, and D. Smith. “Analysis of Persian Painted Mina’i Ware,” “in Scientific Research on Historic Asian Ceramics: Proceedings of the Fourth Forbes Symposium at the Freer Gallery of Art, (Washington D.C.: Archetype Publications in association with the Freer Gallery of Art, Smithsonian Institution, 2009), 33–47.
[15] See Freer DCSR laboratory records for F1943.3. Zycherman’s observations date to 1983.
[16] This observation would imply that the initial efforts at reconstitution and restoration of this plate had numerous mina’i sherds on hand. Common mina’i motifs such as floriated Kufic, landscape elements, horsemen, geometric decoration, and the ubiquitous birds must have been available to be inset as necessary. For example, similar motifs of floriated Kufic are found on: Survey of Persian Art, pls. 676, 694a and b, 695a and b; Ernst Grube, Cobalt and Luster. The Nasser D. Khalili Collection of Islamic Art, vol. IX. (Oxford: Oxford University Press 1994), nos. 227, 229, 233–39; Watson, Ceramics, 2004, 366, 368. Sherds with horse and rider, often from smaller bowls, are common, and two can be found in the Freer Study Collection, FSG-P-4776 and FSG-P-4786. Use of such sherds with profiles different than the much larger mina’i plate would have required the sandwiching inlay technique noted on the Siege Scene Plate.
[17] Holod, “Event and Memory.”
[18] On the Bahram Mirza Album and similar albums as well as painting workshop procedures, see David Roxburgh, The Persian Album, 1400–1600: From Dispersal to Collection (New Haven: Yale University Press, 2005), 3–147.
[19] Pounces may not have been noticed due to loss of the evidence while in the kiln. Carbon black, commonly used for sketches and pounces, would burn and disappear during firing.
[20] Koss et al., “Analysis.”
[21] Holod, “Event and Memory,” 210.
[22] Other pieces showing this kind of expanded polychromy are limited in number. A beginning list of such examples would include: F1945.8; Metropolitan Museum, 57.36.9, 12.49.1; Museum of Fine Arts, Boston, 15.036, 26.28, 31.95. See also Holod, “Event and Memory,” 210, for a discussion of two different practices of color production on mina’i.
[23] Very few samples of magenta have been examined. Koss et al. looked at three and found that two were likely applied after the first firing, while it was not possible to assign the third to a specific firing step; see Koss et al., “Analysis.”
[24] Mason et al., “Advances.”
[25] Koss et al., “Analysis.”
[26] For a recent illustration see: Eleanor Sims with B. Marshak and E. Grube, Peerless Images: Persian Painting and its Sources (New Haven: Yale University, 2002), 93.
[28] Holod, “Event and Memory,” 210, where the sequence of color application is discussed, can now be more clearly restated. In the case of this plate, the magenta color was applied as part of the second phase of decoration to be fixed to the surface in a smoky atmosphere.
[29] The quantitative analyses necessary to determine the composition of the glass phase in any of the colors in this plate have not been carried out at this time.
[30] The brown, red, and magenta on the Siege Scene Plate are adjacent and thus are the product of conscious compositional differentiation, not of firing differences or inconsistencies.
[31] Watson, “Documentary,” 1994, and Ceramics, 2004; Mason, Shine, 154; Pancaroğlu, Perpetual Glory; and Sheila Blair, “A Brief Biography of Abu Zayd,” Muqarnas 25/2008, 155–77.
[32] Koss et al., “Analysis,” 42.
[33] This tile is similar to the central panel of a mihrab originally from the Masjid-i Maidan, Kashan, dated 1226, that is held in the Islamic Museum of the Staatliche Museen zu Berlin, Inv.-Nr. I. 5366 (SPA, vol. 5, pl. 704).
[34] Koss et al., “Analysis.”
"Under a Microscope" is an online component of Ars Orientalis 42, published October 2012.